Mold Manufacturer China: Elevating Manufacturing Standards
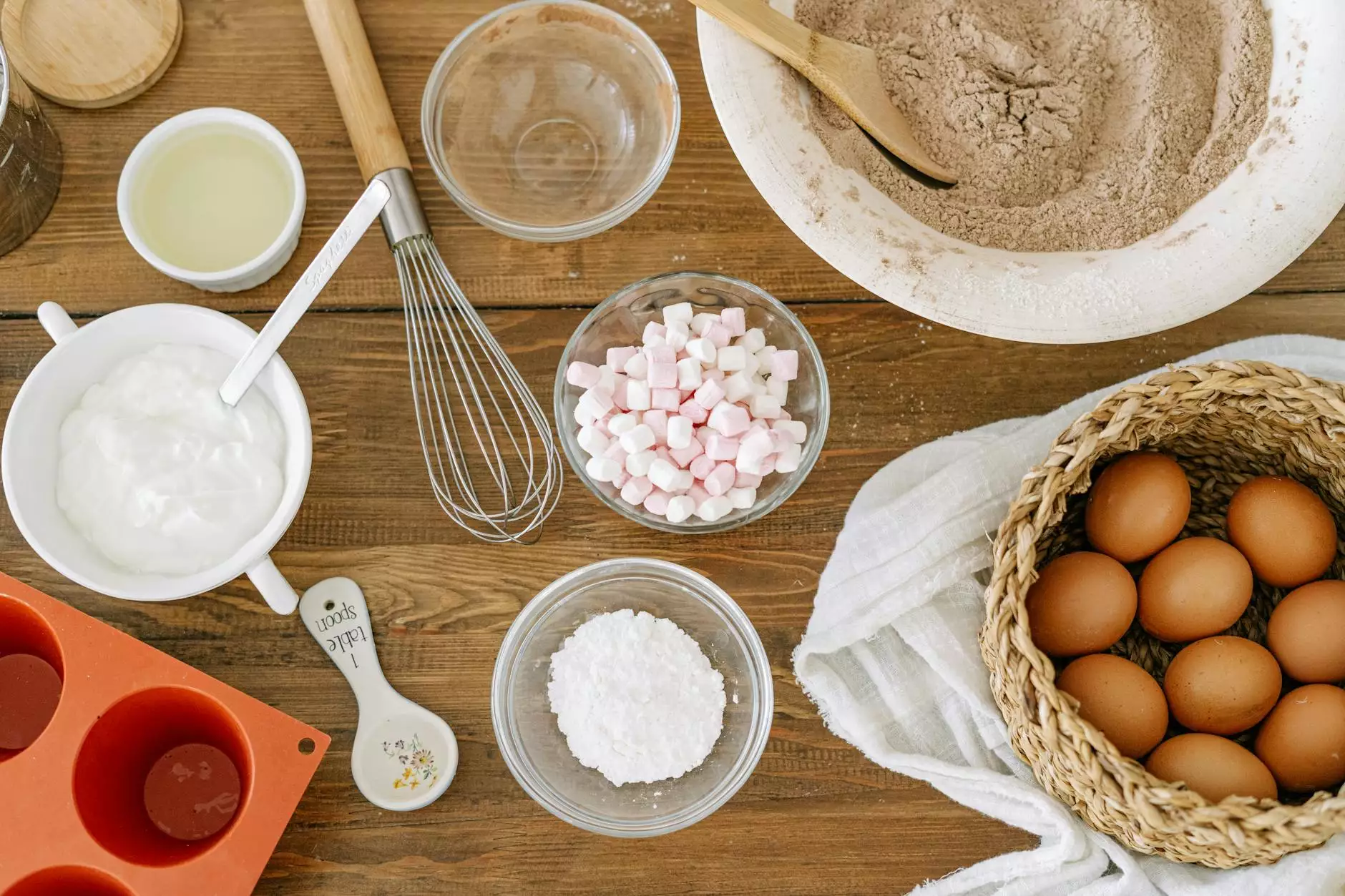
In an era defined by rapid technological advancements and an insatiable demand for efficient production processes, the role of a mold manufacturer in China has never been more critical. China stands at the forefront of global manufacturing, showcasing unparalleled expertise in mold design and fabrication. Companies like DeepMould are leading the charge, setting new standards for quality, agility, and innovation in the mold industry.
The Significance of Mold Manufacturing in Modern Industry
Mold manufacturing is the backbone of numerous industries, including automotive, consumer electronics, and medical devices. The process of creating molds is essential for producing high-quality parts that meet strict tolerances and specifications. Without molds, mass production of intricate designs would be nearly impossible.
Why Choose China for Mold Manufacturing?
When it comes to sourcing molds, many businesses opt for Chinese manufacturers due to several compelling reasons:
- Cost-Effectiveness: Labor and material costs in China are significantly lower, enabling manufacturers to provide competitive pricing without compromising quality.
- Advanced Technology: Chinese mold manufacturers invest heavily in the latest technology, ensuring precision and efficiency in their production processes.
- Skilled Workforce: China boasts a vast pool of skilled engineers and technicians with specialized training in mold design and manufacturing.
- Rapid Production Times: The integration of automation and efficient manufacturing techniques allows for quicker project turnaround, which is vital in today’s fast-paced market.
The Process of Mold Manufacturing in China
Understanding the manufacturing process is essential for any business looking to engage with a mold manufacturer in China. Here’s a comprehensive overview of the typical stages involved:
1. Design and Prototyping
The journey begins with designing the mold. This phase is crucial, as the mold must be engineered to meet the specifications of the end product. Manufacturers often utilize advanced CAD (Computer-Aided Design) software to create detailed models and simulations. Prototyping follows, allowing clients to assess the design before mass production.
2. Material Selection
Choosing the right materials is pivotal. The most common materials for mold making include:
- Steel: Known for its durability and strength, it is often used for production molds.
- Aluminum: Lightweight and cost-effective, ideal for short runs or prototypes.
Each material type has its advantages, depending on the intended use and production volume.
3. Machining and Fabrication
This phase entails the actual manufacturing of the molds. Using state-of-the-art CNC (Computer Numerical Control) machines, mold manufacturers carve and assemble the components with high precision. This careful fabrication ensures that the molds can withstand high pressures and temperatures in production.
4. Testing and Quality Control
Quality assurance is integral to the manufacturing process. After the molds are constructed, they undergo rigorous testing to ensure they meet the necessary specifications and quality standards. Any imperfections are addressed before the molds are shipped to clients.
5. Delivery and Support
Once the molds pass quality inspection, they are packaged and delivered to clients. A reputable mold manufacturer in China, like DeepMould, will also provide ongoing support, helping clients with mold maintenance and troubleshooting any issues that might arise during production.
Key Benefits of Partnering with DeepMould
Choosing the right mold manufacturer can significantly impact your production capabilities. Here’s why DeepMould is a preferred partner for many:
- Expertise and Experience: With years of experience in the industry, DeepMould possesses deep knowledge in mold design and manufacturing, ensuring high-quality outcomes.
- Custom Solutions: DeepMould specializes in providing tailored solutions based on client needs, from design to production.
- Commitment to Innovation: Continuous investment in the latest technologies keeps DeepMould ahead of the competition, enabling better quality and efficiency.
Challenges in Mold Manufacturing
While the mold manufacturing industry in China thrives, it is not without challenges. Some of these include:
1. Quality Consistency
Maintaining consistent quality across all products can be challenging, particularly when scaling production. However, established companies like DeepMould prioritize strict quality control measures, ensuring every mold meets the highest standards.
2. Regulatory Compliance
China’s manufacturing landscape is subject to various international regulations that can change frequently. Staying compliant requires vigilance and expertise—a hallmark of reputable manufacturers.
3. Environmental Considerations
With growing scrutiny on manufacturing processes, it is vital for mold manufacturers to adopt sustainable practices. DeepMould has embraced eco-friendly solutions, reducing waste and energy consumption throughout the manufacturing process.
The Future of Mold Manufacturing in China
As the global demand for high-quality molds continues to rise, the future looks bright for mold manufacturers in China. Emphasizing sustainability, technological advancements, and skilled labor will pave the way for innovative solutions in the industry.
1. Technological Integration
The integration of IoT (Internet of Things) and AI (Artificial Intelligence) into manufacturing processes will revolutionize how molds are designed and produced. Smart factories are setting new standards for efficiency and accuracy, allowing manufacturers to continuously optimize their operations.
2. Expansion into New Markets
As industries evolve, so does the need for innovative molds. Manufacturers are exploring opportunities in emerging technologies such as electric vehicles and smart devices, offering endless possibilities for growth.
3. Enhanced Collaboration
Building strong partnerships between manufacturers and clients will be crucial in addressing specific needs and challenges. DeepMould is committed to fostering collaboration, ensuring that customers receive personalized service and outstanding results.
Conclusion
In conclusion, the landscape of mold manufacturing in China, particularly with companies like DeepMould, signifies a robust ecosystem that combines quality, technological advancement, and expert craftsmanship. For businesses seeking reliable partnerships in mold manufacturing, engaging with a skilled mold manufacturer in China represents a strategic move toward excellence. As the industry continues to evolve, staying at the forefront of innovation and sustainability will ensure ongoing success in the global manufacturing arena.
mold manufacturer china